Cutting-edge Material Development
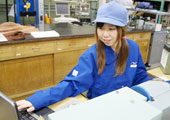
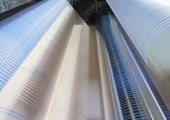
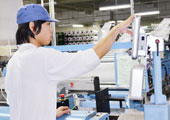
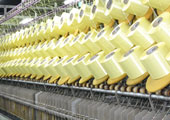
Exploration and enhancement of fundamental technology
Our main products are reinforcement cords for rubber products. For example, reinforcement cords that act as the skeleton of a tire, known as tire cords. In automobiles, the brake hoses that direct brake fluid, air conditioner hoses that circulate refrigerant gas, and radiator hoses that circulate coolant all utilize reinforcement cords. In addition, timing belts and V-belts contain reinforcement cord to prevent elongation. Our technology is used in a wide range of vehicles from the ordinary cars you see around town, to racecars.
We choose the appropriate fibers for the application and part, then use twisting and heat setting to craft the optimal cord. Figure 1 shows an example of the stress–strain curves (strength elongation curves) for the products we are developing and those we have brought to market. The strength units in Figure 1 are MPa for strength by area, and cN/dtex for strength by mass (in the fiber industry the dtex number shows the mass per 10,000 m of length expressed in grams, and is called "fineness"). The meaning of "strength" can be understood in various ways.
Figure 1. Example stress–strain curves for our products and in-development products
- Fibers
-
In general, synthetic fibers are composed of multiple single strands (filaments). These filaments are composed of a collection of fibers called macrofibrils, which are in turn composed of a collection of fibers called fibrils. Fibrils themselves are composed of a collection of fibers called microfibrils. Microfibrils are composed of multiple molecular chains of polymers. Their relative sizes are shown in Figure 2. Microfibrils are on the order of 0.01 mμ or 10 nanometers. At first we wrote "composite fibers," but in fact, the structure of these is much the same as that of hair. This is quite amazing considering how differently synthetic and natural fibers are made.
By controlling the conditions of microfibrils on a nano-scale, we can create different fabric properties. Even when using the same polymer, its properties can be adjusted by controlling manufacturing conditions and heat treatment during adhesive processing. We have even explored silk making conditions in cooperation with silk producers, in order to produce the optimum product for our customers.Figure 2. Fiber structure
according to "Sawyer, L.C. & Jaffe, M (1986) The structure of thermotropic copolyesters, Journal of Materials Science, 21, 1897-1913" - Adhesives
-
In order to obtain a reinforcement effect for strong cords, it is not enough to just embed fibers in the rubber. The fibers and rubber must be bonded together. And because both the rubber and fibers deform greatly, the adhesive must be able to handle this deformation.
For years, resorcinol-formaldehyde resin and latex rubber mixture (also known as RFL) has been used to bond the fibers to the rubber. The raw materials of resorcinol-formaldehyde resin (RF resin) are simple. They are just resorcinol (C6O2H6), formaldehyde (HCHO) and a catalyst. However, the same material will produce a wide variety of RF resins depending on the mixing ratio and reaction conditions.
The resorcinol and formaldehyde reaction contains an addition reaction (dehydration condensation) between resorcinol and formaldehyde, and a condensation reaction between resorcinol and itself. Acid catalysts promote the condensation reaction, forming novolac-type RF resin (thermoplastic resin; softens when heated and hardens again when cooled). Alkaline catalysts promote the addition reaction, forming resol-type RF resin (thermosetting resin; hardens when heated and does not soften again).
Adhesive is made by adding adhesion aids such as latex rubber and blocked isocyanate to the RF resin. The finished adhesive can stretch to follow the deformation of the materials as in the stress–strain curve shown in Figure 3, while still maintaining the adhesive bond between the rubber and fibers.
This allows for a large degree of design freedom, enabling the ideas of developers to be reflected directly in product capabilities. And while we can't explain the details here, if the RF resin is produced under special environmental conditions, it's possible to make RFL that remains stable for many years without losing its adhesive properties.Figure 3. Adhesive stress–strain curve example
- In conclusion
-
Along with developing new products and processes, Toray Hybrid Cord, Inc. aims to research and enhance the fundamental technology that is the basis of our business.